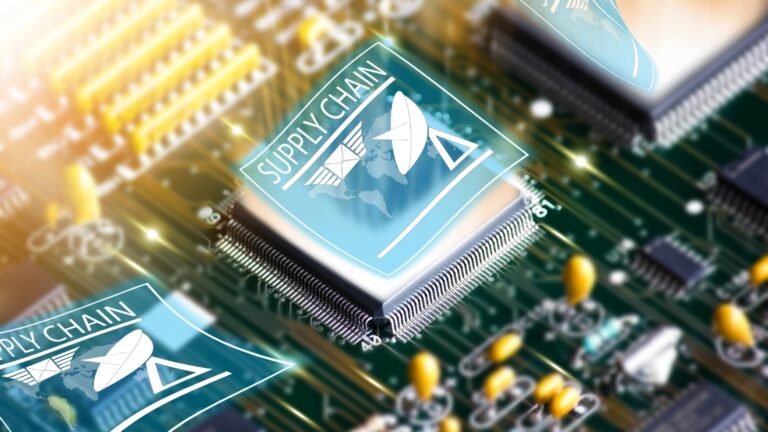
In today’s globalized economy, supply chains are more interconnected and complex than ever before. While these connections help businesses meet the growing demands of consumers, they also expose supply chains to a range of potential risks. From natural disasters and pandemics to geopolitical conflicts and cyberattacks, disruptions can arise from almost anywhere, severely impacting businesses’ operations. To navigate these challenges, companies need to build supply chain resilience by implementing robust risk management strategies. In this article, we’ll explore the importance of supply chain resilience, the role of risk management, and practical steps for ensuring continuity in uncertain times.
What is Supply Chain Resilience?
Supply chain resilience refers to a company’s ability to anticipate, prepare for, respond to, and recover from disruptions. A resilient supply chain can maintain continuous flow despite unexpected setbacks, reducing the likelihood of operational downtime and revenue loss. In today’s volatile environment, where disruptions can arise without warning, resilience is no longer a luxury but a necessity.
Businesses face a variety of risks that threaten the smooth operation of their supply chains. For instance, natural disasters such as hurricanes, earthquakes, and floods can destroy manufacturing facilities and interrupt transportation networks. On the other hand, pandemics like COVID-19 can lead to labor shortages and factory shutdowns, while geopolitical tensions or trade wars can create delays due to regulatory changes or tariffs. All these factors contribute to why resilience is critical for maintaining a stable supply chain.
The Role of Risk Management in Supply Chain Resilience
A resilient supply chain doesn’t just happen by chance—it requires effective risk management. Risk management is the process of identifying, assessing, and mitigating risks that could affect a company’s operations. Here’s how risk management contributes to building a resilient supply chain:
Identifying Supply Chain Risks
The first step in risk management is identifying the risks that could impact the supply chain. These risks can be internal, such as production bottlenecks or supplier insolvency, or external, like natural disasters, global health crises, or economic downturns. By systematically identifying these risks, companies gain a clearer understanding of the vulnerabilities in their supply chains.
Common categories of supply chain risks include:
- Environmental Risks: Natural disasters, climate change, and extreme weather events.
- Geopolitical Risks: Trade restrictions, regulatory changes, and political instability.
- Operational Risks: Labor shortages, transportation failures, and supplier performance issues.
Risk Assessment and Prioritization
Once risks are identified, the next step is to assess their likelihood and potential impact. Not all risks will have the same effect on a business. By prioritizing risks based on their severity, companies can focus on those that pose the greatest threat to their supply chains. Risk assessment tools, such as scenario analysis and impact modeling, help businesses anticipate how different risks might affect their operations, enabling them to prepare accordingly.
Mitigation Strategies
After assessing the risks, companies must implement mitigation strategies to reduce their potential impact. These strategies can range from diversifying suppliers and creating inventory buffers to leveraging technology that enhances visibility and responsiveness. Here are a few common mitigation strategies:
- Supplier Diversification: Relying on a single supplier or region for critical materials can leave a company vulnerable to disruptions. By diversifying suppliers across different locations, companies can minimize risk and ensure supply continuity.
- Inventory Buffers: Holding extra inventory or safety stock allows companies to maintain production during periods of supply shortages. However, it’s essential to strike a balance, as excess inventory can increase storage costs.
- Technology Adoption: Digital tools like IoT, blockchain, and AI-powered analytics provide real-time insights into supply chain operations. These tools help businesses identify potential risks earlier and react faster when disruptions occur.
Building a Resilient Supply Chain: Key Elements
Building a resilient supply chain requires a holistic approach that goes beyond just managing risks. It involves creating flexibility, fostering collaboration, and investing in technologies that improve agility and adaptability.
Flexibility and Adaptability
A resilient supply chain must be flexible enough to adapt to changes in demand, supplier availability, and logistical constraints. Flexibility can be achieved by maintaining alternative suppliers, using multiple transportation modes, and adopting flexible manufacturing processes. This adaptability allows businesses to quickly pivot and adjust their operations when faced with unexpected challenges.
Collaboration and Communication
Strong communication and collaboration with suppliers, partners, and stakeholders are essential for building a resilient supply chain. Establishing transparent and open lines of communication helps businesses identify risks early and respond faster. Additionally, collaborating with key partners can create mutually beneficial risk-sharing agreements, such as collaborative forecasting, where suppliers and buyers work together to predict future demand and plan accordingly.
Investing in Technology
The right technology can significantly enhance supply chain resilience. Tools such as predictive analytics, artificial intelligence (AI), and Internet of Things (IoT) devices enable businesses to monitor and manage their supply chains in real time. For instance, predictive analytics can help companies forecast potential disruptions, while IoT sensors track shipments and inventory levels in real time, providing greater visibility into the supply chain. This visibility allows companies to respond proactively, whether it’s rerouting shipments or adjusting inventory to match demand.
Real-World Examples of Supply Chain Resilience
Many companies have already implemented robust risk management strategies to build supply chain resilience, especially in response to recent global events.
For example, during the COVID-19 pandemic, Apple faced significant supply chain disruptions due to factory closures in China. To mitigate the impact, Apple diversified its supplier base and invested in digital tools to track inventory and production more effectively. As a result, the company was able to maintain continuity in its operations, even as global supply chains struggled.
Similarly, Toyota is well-known for its commitment to supply chain resilience. After facing a devastating earthquake and tsunami in 2011, Toyota redesigned its supply chain to be more flexible, adopting a “just-in-case” inventory model that allowed it to maintain production in the face of future disruptions. Toyota also improved its communication with suppliers, enabling faster response times to unexpected events.
Practical Steps for Implementing Supply Chain Risk Management
Here are some actionable steps businesses can take to strengthen their supply chain resilience through risk management:
- Risk Identification Tools: Implement software that identifies potential risks across the supply chain. These tools can provide insights into environmental, operational, and geopolitical risks.
- Risk Monitoring Systems: Use real-time monitoring systems, such as IoT sensors and AI-driven analytics, to track the status of suppliers, shipments, and inventory levels. This enables quick responses to disruptions and improves decision-making.
- Business Continuity Planning: Develop a comprehensive business continuity plan that outlines how the company will respond to various risks, including alternative suppliers, backup transportation routes, and contingency plans for critical resources.
- Regular Risk Assessments: Continuously assess risks and revisit mitigation strategies to ensure they are effective. Supply chains are dynamic, so regular evaluations are essential for maintaining resilience.
Conclusion
In an increasingly unpredictable world, building supply chain resilience through effective risk management is critical for ensuring business continuity and long-term success. By identifying risks, prioritizing them, and implementing mitigation strategies, companies can create supply chains that are not only more robust but also more adaptable to change. Investing in technology, fostering strong supplier relationships, and maintaining flexibility will empower businesses to weather future disruptions with confidence.
Proactive risk management is the foundation of a resilient supply chain, and businesses that prioritize it will be well-positioned to thrive, no matter what challenges come their way.