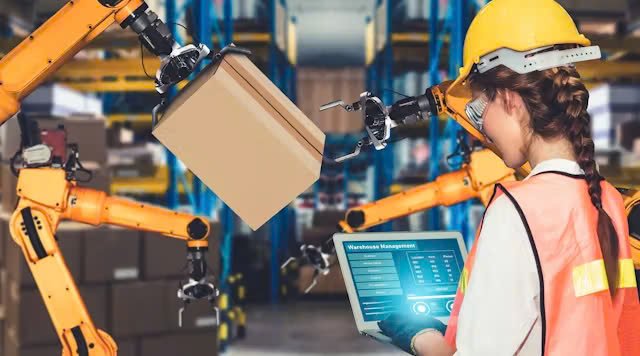
In today’s fast-paced industrial environment, robotics has revolutionized manufacturing, transforming production processes, increasing productivity, and improving workplace safety. This transformation is reshaping how industries operate, making processes more efficient and allowing businesses to stay competitive. With companies like Emperor Brains, businesses can leverage cutting-edge robotics solution
The Rise of Robotics in
The integration of robotics in manufacturing isn’t new, but it has undergone dramatic advancements in recent years. Early robots were designed to handle simple, repetitive tasks such as moving parts or assembling components. However, as technology evolved, the rise of Artificial Intelligence (AI),machine learning, and sensor technology has significantly expanded the capabilities of these machines.
Today’s robots aren’t limited to simple tasks; they can perform highly intricate operations with remarkable precision. Modern robots are equipped with advanced algorithms and enhanced sensors, enabling them to adapt to different environments and perform a variety of tasks that were once thought impossible for machines. This growth in capability is driving the widespread adoption of robotics in various industries.
Types of Robots Used in Manufacturing
There are various types of robots designed for specific tasks in the manufacturing sector. Here’s a look at the most prominent ones:
1. Industrial Robots
Industrial robots are the backbone of automated manufacturing. These machines are typically deployed for tasks such as welding, painting, assembly, and material handling. Their ability to operate at high speeds with pinpoint accuracy makes them an ideal choice for mass production. With the ability to function 24/7 without breaks, industrial robots can significantly reduce downtime and boost productivity.
2. Collaborative Robots (Cobots)
Cobots are designed to work alongside human workers. Unlike traditional robots, which are often isolated from humans due to safety concerns, cobots come equipped with advanced sensors and safety features that allow them to safely interact with people. They are especially valuable in environments where human dexterity is still needed but can be complemented by robotic strength and precision. Cobots are becoming increasingly popular in industries requiring a high degree of flexibility and human-robot interaction.
3. Autonomous Mobile Robots (AMRs)
AMRs are mobile robots designed to move materials within a facility. Unlike traditional robots that follow predefined paths, AMRs are equipped with sensors, cameras, and AI-driven navigation systems, enabling them to traverse complex environments independently. These robots can adjust their routes in real-time to avoid obstacles, which makes them especially useful in dynamic environments like warehouses or factories where floor plans may change frequently.
4. Articulated Robots
Articulated robots feature multiple rotating joints, making them highly flexible and capable of performing a wide range of tasks. These robots are particularly useful in assembly, material handling, and welding. Their flexibility allows them to reach into tight spaces and maneuver in ways that static robots cannot, making them a popular choice for more intricate manufacturing processes.
5. SCARA Robots (Selective Compliance Articulated Robot Arm)
SCARA robots specialize in tasks requiring precise lateral movement, such as assembly, packaging, and palletizing. Their rigid design in the vertical axis allows for fast and precise movement along the horizontal axis, making them ideal for tasks requiring high speed and accuracy.
Benefits of Robotics in Manufacturing
The integration of robotics offers numerous advantages that can significantly enhance the overall performance of manufacturing operations. Here’s a closer look at how robotics benefits modern manufacturing:
1. Increased Productivity
One of the most significant benefits of using robotics in manufacturing is the dramatic boost in productivity. Robots can work around the clock, performing repetitive tasks at a much faster rate than human workers. This eliminates delays caused by fatigue or human error and helps manufacturers achieve higher production rates with consistent quality.
2. Enhanced Product Quality
Robots are known for their precision and consistency. By removing the potential for human error, manufacturers can significantly reduce product defects. Robotics ensures that every product is made with the same level of accuracy, resulting in higher-quality products and improved customer satisfaction.
3. Cost Savings
Although the initial investment in robotics may seem high, the long-term savings are substantial. Robots reduce labor costs, minimize material waste, and improve overall operational efficiency. By streamlining production processes, manufacturers can lower their costs per unit, making them more competitive in the global market.
4. Improved Safety
Many manufacturing tasks involve working in hazardous conditions, such as handling dangerous chemicals, performing heavy lifting, or working in extreme temperatures. Robots can take on these dangerous jobs, keeping human workers out of harm’s way and reducing the risk of workplace injuries.
5. Flexibility and Scalability
Modern robots are highly adaptable and can be reprogrammed to handle a variety of tasks. This flexibility allows manufacturers to scale their operations and quickly respond to changing market demands. As consumer preferences shift or new products are introduced, robotic systems can be adjusted to meet new requirements with minimal downtime.
Real-World Applications of Robotics in Manufacturing
Robotics has become a key component in several industries, driving efficiency and innovation. Let’s explore some examples:
- Automotive Industry: Robots are widely used for welding, assembly, and painting tasks. These machines ensure consistent production quality and reduce the time required to manufacture vehicles.
- Electronics Manufacturing: In electronics, robots are responsible for assembling delicate components, soldering, and testing devices. Their precision is essential in producing small, intricate electronic products.
- Food and Beverage Industry: The food industry relies on robotics for packaging, palletizing, and quality control. Robots help maintain strict hygiene standards and increase the efficiency of production lines.
- Pharmaceutical Industry: Robots in this industry are used for tasks like mixing ingredients, filling containers, and packaging medicines. Their accuracy and consistency are vital for ensuring product safety.
- Metal Fabrication: Robotics plays a significant role in metal fabrication, where they are used for welding, cutting, and material handling. Robots not only improve the quality of finished products but also enhance worker safety by taking on hazardous tasks.
Challenges of Implementing Robotics in Manufacturing
While robotics offers numerous benefits, there are also challenges to consider:
- High Initial Investment: The cost of purchasing and installing robotic systems can be high. However, the long-term benefits usually outweigh the initial costs.
- Technical Expertise: Operating and maintaining robotic systems requires specialized knowledge. Manufacturers must invest in training their workforce or hire experts to ensure smooth operations.
- Integration with Existing Systems: Seamlessly integrating new robotic systems with existing production lines can be complex. Proper planning is essential to ensure minimal disruptions during the transition.
- Workforce Impact: The rise of robotics has led to concerns about job displacement. However, many manufacturers are addressing this by reskilling workers to collaborate with robots, focusing on tasks that require human creativity and decision-making.
The Future of Robotics in Manufacturing
The future of robotics looks incredibly promising. Here are some key trends to watch for:
- AI and Machine Learning: Robots will continue to evolve, becoming even more autonomous and capable of making real-time decisions. This will further enhance their efficiency and capabilities.
- Human-Robot Collaboration: As cobots become more advanced, they will work more closely with human workers, leading to safer and more productive workplaces.
- Industry 4.0 and IoT: The integration of IoT technologies will improve connectivity between robots and other systems, leading to better data collection, analysis, and decision-making.
- Sustainability: Robotics will play a vital role in driving sustainable manufacturing practices by reducing waste, improving energy efficiency, and enabling the production of eco-friendly products.
Conclusion: Embracing Robotics with Emperor Brains
The integration of robotics in manufacturing is not just a technological advancement; it’s a revolution that is reshaping the industrial landscape. By adopting robotics, manufacturers can achieve unprecedented levels of productivity, quality, and safety. At Emperor Brains, we are at the forefront of this transformation, offering tailored robotic solutions to help our clients stay competitive